Disposable Medical Connector Contact Technologies
Single-use equipment that can be tossed instead of sterilized is in demand for some types of procedures or environments. The connectors inside these devices must be reliable, durable, and affordable.
By Roberta Rebora, Marketing Communications Director, Smiths Interconnect
Due to growing concerns about spreading disease from patient to patient via improperly or inadequately sterilized devices, the idea of disposable medical devices is very attractive. Just as a disposable hypodermic syringe eliminates the possibility of this type of disease transmission, disposable medical electronics, such as invasive electronic probes, would be used just once instead of being autoclaved between procedures, eliminating both the contamination risk, as well the need for components capable of withstanding repeated sterilization cycles.
One example of this type of disposable electronic device is an electrophysiology catheter, which is inserted through a small incision in a blood vessel (e.g., in the groin) and then pushed through to the interior of a patient’s heart to ablate (i.e., burn) select tissue to treat arrhythmias. To prevent the possibility of transmitting germs to the next patient, device manufacturers specify that these catheters are single-use devices that must be disposed of after use. In fact, to limit liability, manufacturers will typically void the warranty of these devices if it they are sterilized and reused.
Driving Factors
Today, several factors go into determining whether a medical device — and, by extension, the connectors therein — should be disposable or reusable. The costs of the materials used in the device and the effects of sterilization on the device must be counterbalanced with concerns about the efficacy of sterilization processes and adding to the waste stream with single-use disposable devices. Reusable devices and their enabling interconnects can be, and generally are, more expensive than disposable devices on a per-unit basis. This is due to the fact that they employ materials and manufacturing methods designed to ensure that they maintain peak performance under the rigors of repeated use, high mating and unmating cycles, and disinfection and sterilization protocols. Disposable devices and their enabling connectors, on the other hand, are required to work just one time, with one patient, and then be thrown out, requiring end-users to buy one device (or set of devices) for every procedure.
Cost is an important element of the reusable or disposable device decision, and the connector cost is just a part of that equation. Another consideration is the termination of the connector on the disposable device to the connector on the reusable portion of the equipment. Limiting the number of operations required to terminate the connector can help reduce the applied cost of the device. Although the connector on the disposable side of a device only has to operate once, it has to mate with the connector on the reusable side without causing the reusable connector to fail over its rated mating lifecycle. Although disposable connectors must be just as reliable as reusable connectors, they only require that level of reliability for a single cycle.
Four Contact Technologies
A number of interconnect technologies offered by leading connector companies are used in connectors for disposable applications. Four such interconnect technologies: screw machined hyperboloid contact systems, stamped hyperboloid contacts, spring probes, and edge-card contacts. Each of these options feature unique characteristics designed to address the specific application, cost, and performance requirements for disposable medical electronics.
Hyperboloid Contacts
Screw-machined hyperboloid contacts employed in a reusable connector can provide unrivaled performance with low insertion and extraction forces, high current ratings, low contact resistance, immunity to shock and vibration, and high rated mating lifecycles when mated to low-cost, drawn male pins in a disposable connector. These contacts help reduce overall device cost while maintaining high reliability in the reusable device, ensuring many thousands of successful matings with the simpler disposable connectors. This design also allows the disposable side to be mass terminated to a flex circuit to further reduce the applied costs of the device.
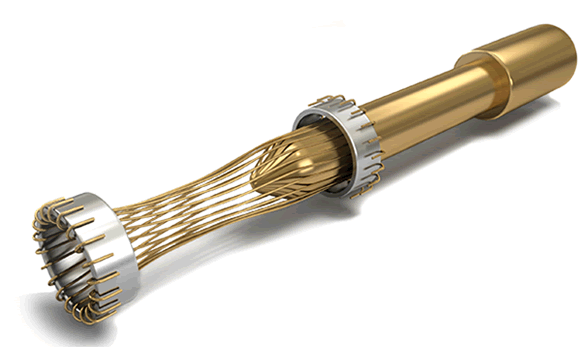
Figure 1: High-density Hypertac® hyperboloid contacts from Smiths Interconnect offer superior signal integrity, high mating cycles, high current ratings, minimal contact resistance, immunity to shock and vibration, and self-cleaning capabilities.
Stamped Hyperboloid Contacts
Sometimes, the reusable components of medical devices, like the extension cables used to connect reusable equipment to single-use probes and catheters, are classified as limited-use parts due to eventual degradation that results from sterilization processes. Stamped hyperboloid contacts are ideal for use in these types of limited-use applications because they provide many of the advantages of screw-machined hyperboloid contacts, including high-reliability wire and insulation, crimped connections, tape and reel packaging for compatibility with crimping machines with automatic feeder lines, and interchangeability and intermateability with screw-machined hyperboloid contacts — but at a lower price point, enabling their use in devices that are used several times before being discarded and replaced.

Figure 2: Stamped hyperboloid contacts from Smiths Interconnect are ideal for high-volume applications that utilize a fully automated process, like the single-use painless needle pictured here.
Spring Probes
Spring probes are well known as test equipment interconnects, but the same attributes that make them ideal in board testers are also perfect for mating to disposable medical devices. For instance, their ability to be manufactured in extremely small diameters makes developing extremely high-density connectors, with many individual contacts in reasonably sized plugs, very feasible. Spring probe technology also permits a high compliance-to-length ratio, which allows manufacturers to design connectors as dense as 2mm while maintaining 0.5mm of compliance. These connectors tend to be low-profile as well, which can make them more forgiving of challenging mating conditions and high-vibration environments. Plus, when employed in disposable medical devices, these connectors can be made to include either low-cost target contacts or to incorporate a low-cost PCB, allowing the spring probes to mate directly to traces on the board.
Speeds of 12Gb/s and bandwidths of 20GHz can be achieved with spring probe interposers, and these connectors are compliant on the surface of their mating half, rather than extending into it, as is the case with conventional pin and socket connectors, providing spring probes with unique blind-mating capabilities. So, a short signal path, combined with design and signal integrity expertise, can ensure remarkable spring probe connector performance in both analog and digital applications.
Edge Card Contact Technology
Edge card connectors offer another ideal solution for low-cost, limited-use, or disposable medical devices. These connectors are customizable, scalable, easy to assemble, and capable of high-density configurations. Additionally, since the PCB, which is typically part of the disposable side of a device, serves as the connector contact, it eliminates the cost of the contact system on the disposable side. Their plug-and-play design also provides effortless termination and virtually eliminates the potential contact damage typically associated with the termination process.
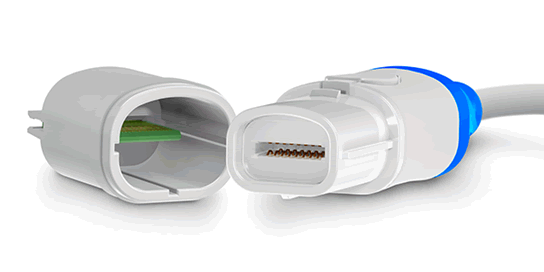
Figure 3: Eclipta connectors from Smiths Interconnect feature edge card contact technology and are ideal for medical applications, including mass terminating catheter wires directly to a PCB.
Another benefit to edge card connectors is their ability to allow designers to add active surface mount components to either side of the PCB to enhance device functionality. An operating temperature range of -10°C to +65°C allows for use in devices that are subject to a variety of environments. High mating cycle capabilities of up to 2,500 cycles increase the mean time between failure (MTBF) and finger-proof contacts on the reusable side contribute to the safety of both patients and medical personnel.
Visit Smiths Interconnect online.
Interested in a specific market? Click a market below for current articles and news.
Automotive, Consumer, Industrial, Medical, Mil/Aero, Datacom/Telecom, and Transportation